Four Key Elements to Ensure Lock Quality—No More Procurement Worries!
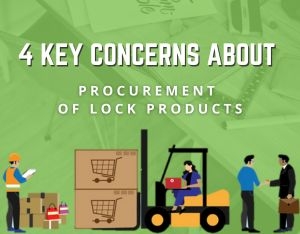
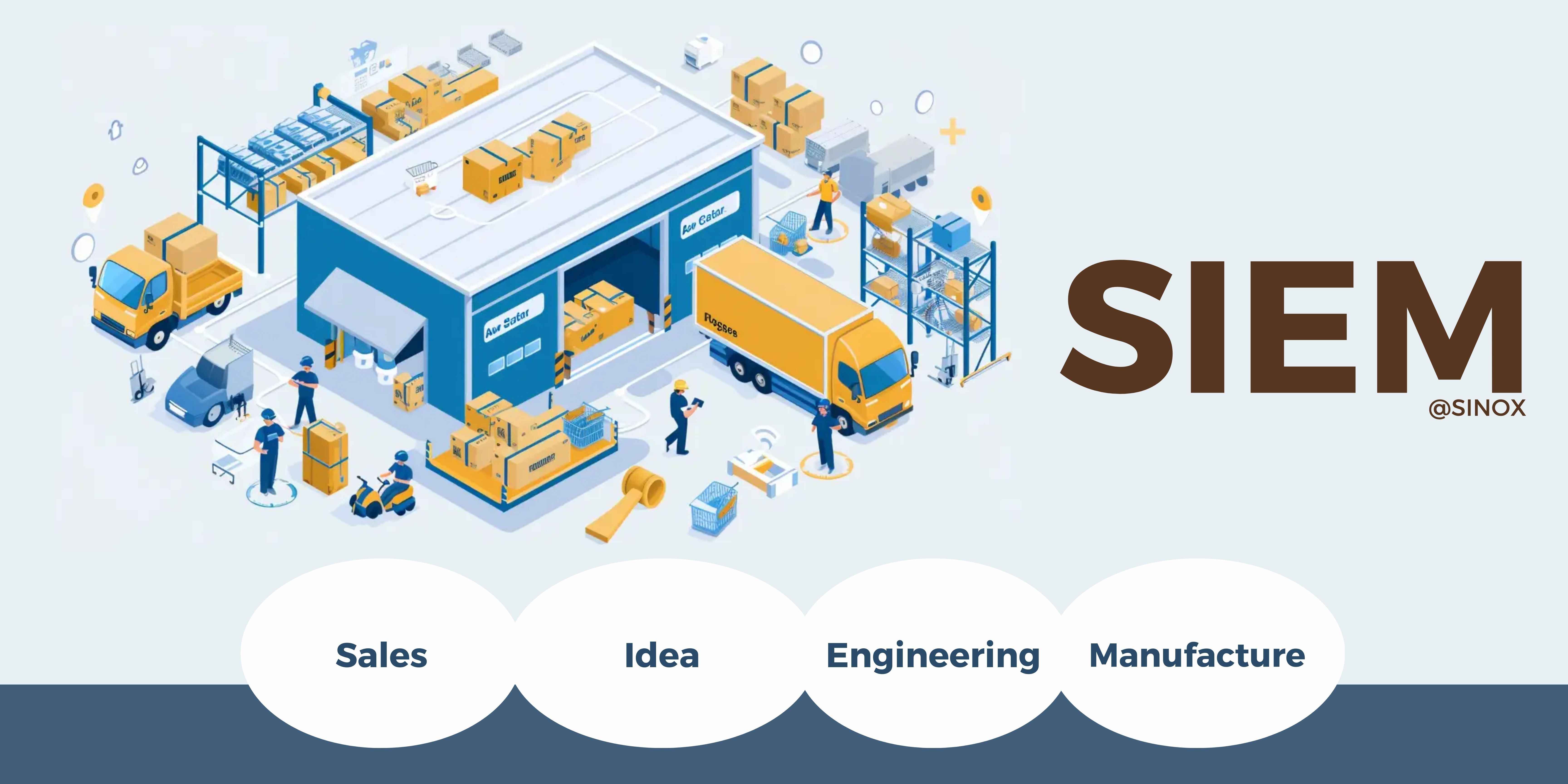
"Why was the quality promised to be superb initially, and the sample looked fine, but during mass production, they said the cost was too high?"
"During the sales pitch, they exaggerated everything, but when it came to design, they said it couldn’t be done. Was it all just an overpromise?"
"Everything was agreed upon during development—production volume and timelines—yet nothing was delivered in the end. Am I just unlucky?"
Have these unfortunate events ever happened to your company?
Procurement managers or project managers are key figures when customizing locks with manufacturers. This process involves extensive preliminary work, communication with suppliers, scheduling, logistics, and more. However, finding the right partner to help your company or brand stand out in the market and create a "dream lock" tailored for your company isn’t difficult at all!
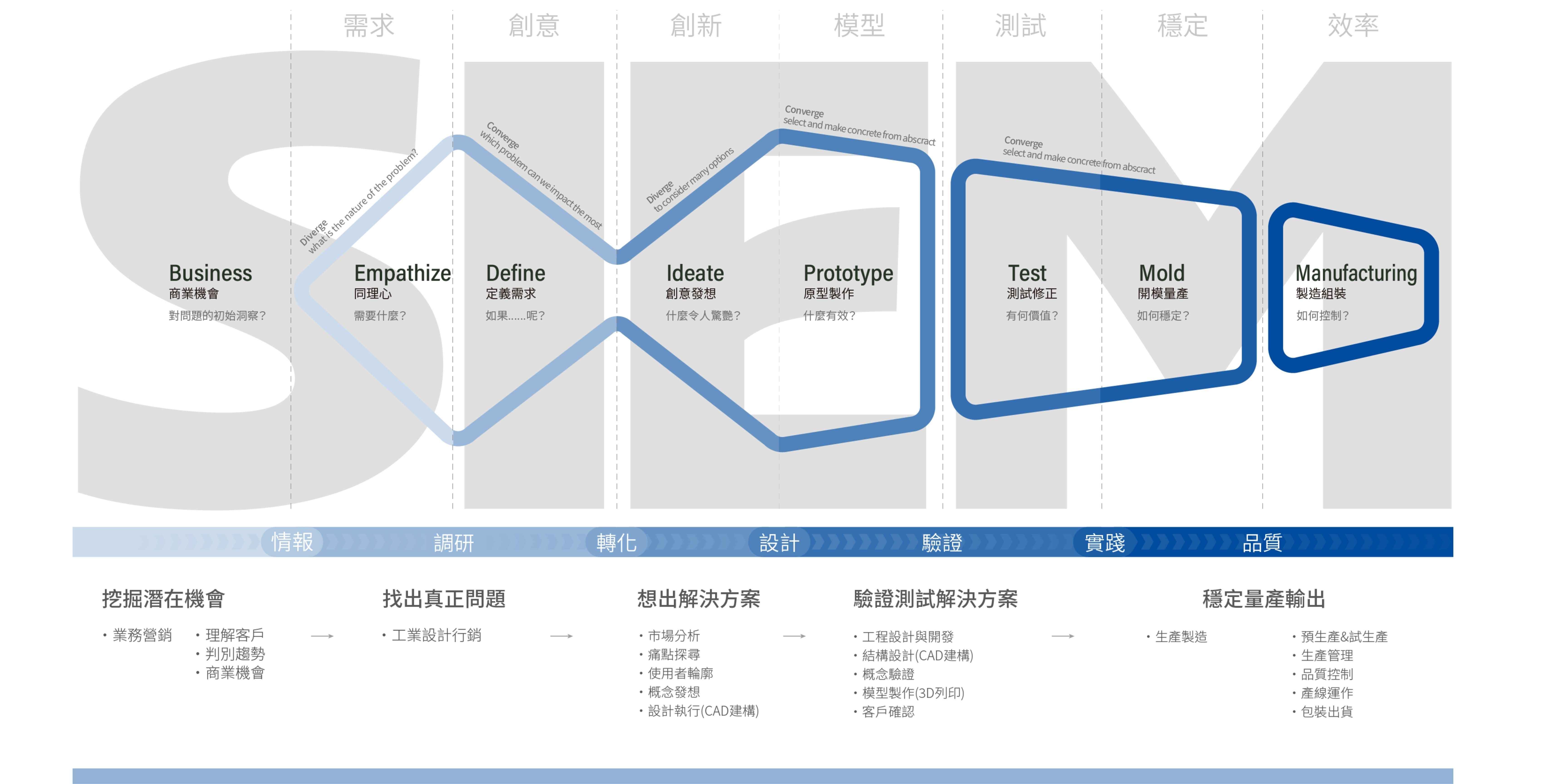
SINOX’s Four Key Processes Build a 46-Year-Strong Reputation
At the critical stage of lock procurement, choosing the wrong supplier can result in unstable product quality and affect the company's overall image and market share!
Imagine if the supplier's product fails safety tests, causing mass production delays, or if the final product doesn't meet quality expectations. Can it be successfully salvaged in time?
When such risks arise, they may cause irreparable damage to your brand's reputation. To address these potential issues, SINOX has developed the SIEM (Sales, Idea, Engineering, Manufacture) core process, specifically designed to optimize lock procurement. This process focuses on information security incident management, helping clients improve quality control and production efficiency when setting lock specifications and standards.
Three Key Benefits of SIEM for Managing Lock Customization Risks
SINOX’s unique SIEM system offers three key advantages, ensuring quality standards while giving room for product creativity:
- Risk Prediction and Control: By integrating various information sources, SIEM can identify potential risks with suppliers early and respond promptly.
- Informed Decision-Making: Using past market and company data for analysis and simulations, SIEM can predict potential issues during procurement and provide optimal solutions.
- Process Optimization: The SIEM process ensures that lock design, testing, manufacturing, and quality control proceed smoothly, reducing unnecessary delays and mistakes.
Breaking Down the SIEM Process
On the sales front (S), initial insights are gathered by considering the customer’s needs, understanding pain points and challenges during actual lock usage, and determining the product design direction accordingly.
The design department (I) then defines requirements based on market research and customer feedback, specifying the lock’s functions and performance and translating them into design standards.
The R&D team (E) assesses the feasibility and benefits of each option through mechanisms and modeling, selecting the most suitable product structure for the client.
Finally, the production team (M) strictly manages production and quality control, ensuring stable mass production for clients.
This process not only enhances the product’s market adaptability but also ensures its functionality and durability, providing clients with high-quality, customized lock solutions that meet real-world needs.
Still Worried About Your Supplier? SINOX Precisely Meets Your Needs
SINOX has successfully served clients from various industries, including HP, TUMI, Decathlon, and Giant. From design to production, the SINOX team follows the stringent SIEM process to ensure every product meets the highest quality standards. If you're struggling with lock procurement or have questions about creating a custom lock, SINOX is ready to offer you the best services and solutions.
[Consult Us: How to Create Your Own Custom Lock]
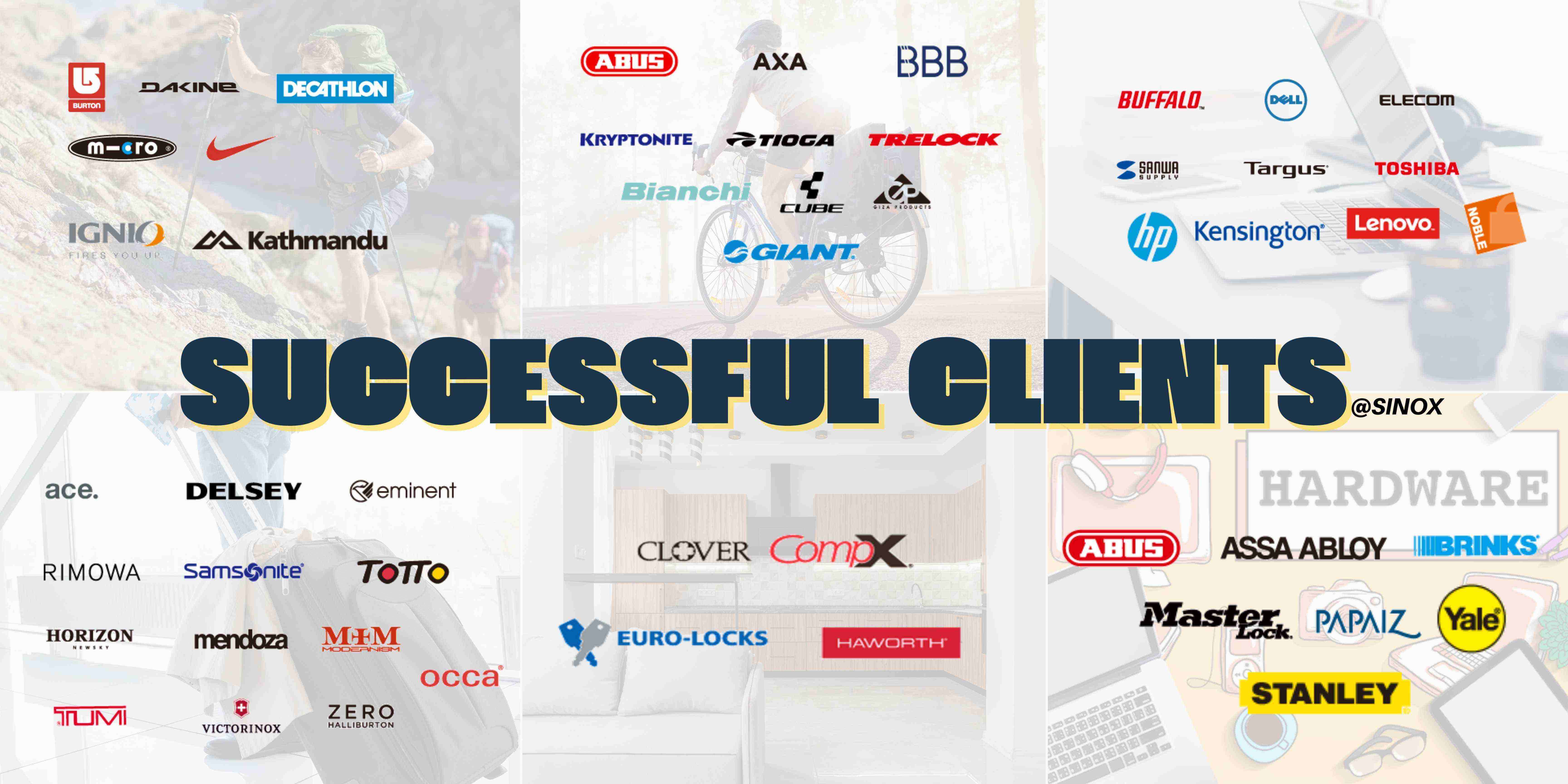